Maker Club Pin Pivots To Improve Snap Together 3d Printed Parts
Maker Club Pin Pivots To Improve Snap Together 3d Printed Parts The gap in the pin needed to be wide enough at the tip to allow it to compress enough to get the wider tip through the narrower receiving hole. the top side of the pin legs were flattened just to simplify the printing and reduce the surface area of the touching parts when inserted and pivoting. the measurement from pin head to pin insertion tip. Model 1: inter lock. this first experiment was actually quite successful in some ways. the linkage parts of each individual object start out being printed separately from it's parent, but then slowly angle toward the parent object until they connect on the top layers. with just about 0.3mm between the interlocking parts, the printer handled.
Maker Club Pin Pivots To Improve Snap Together 3d Printed Parts Saving time (and sanity) with snap together 3d print models. i’ve created many models which include multiple parts that snap together after printing. there are several benefits which drive me to do this so often. first, it allows you to print in more than one color since each part can be printed in its own filament color. 3d printing snap together parts a journey. early in my journey of #3dprinting, i started experimenting with modeling and printing snap together parts. i had a few motivators, as i've mentioned in a previous post, including the ability to make multi color objects, larger objects and objects which had some dynamic properties, like adjustments. For pla the typical value for this is 8%. abs is 10%, petg is 24% and nylon is 100%. simplistically, you could assume that a petg piece could deform up to 25% before breaking. that may be true. Use the right build direction. the layer direction determines the strength of fdm printed parts to a large extent. for the best results, print the layers of the connectors parallel to the joint. so, instead of building the connectors vertically upwards, build them horizontally across the build plate.
.jpg)
Maker Club Pin Pivots To Improve Snap Together 3d Printed Parts For pla the typical value for this is 8%. abs is 10%, petg is 24% and nylon is 100%. simplistically, you could assume that a petg piece could deform up to 25% before breaking. that may be true. Use the right build direction. the layer direction determines the strength of fdm printed parts to a large extent. for the best results, print the layers of the connectors parallel to the joint. so, instead of building the connectors vertically upwards, build them horizontally across the build plate. 3d printing snap fit joints: how to design & print them. by lucas carolo. published feb 28, 2022. snap fit joints are a great solution for part assembly. read about designing and 3d printing snap fit joints, and more, in this guide. Here are a few different ways that i've made parts that connect in the past: example 1: utilize the elasticity of the plastic by creating a semi circle to fit around another object. when fitting the part to the other object, the "wings" will flex out and relax around the back end of the object. example 2: t slot style designs are a nice choice.
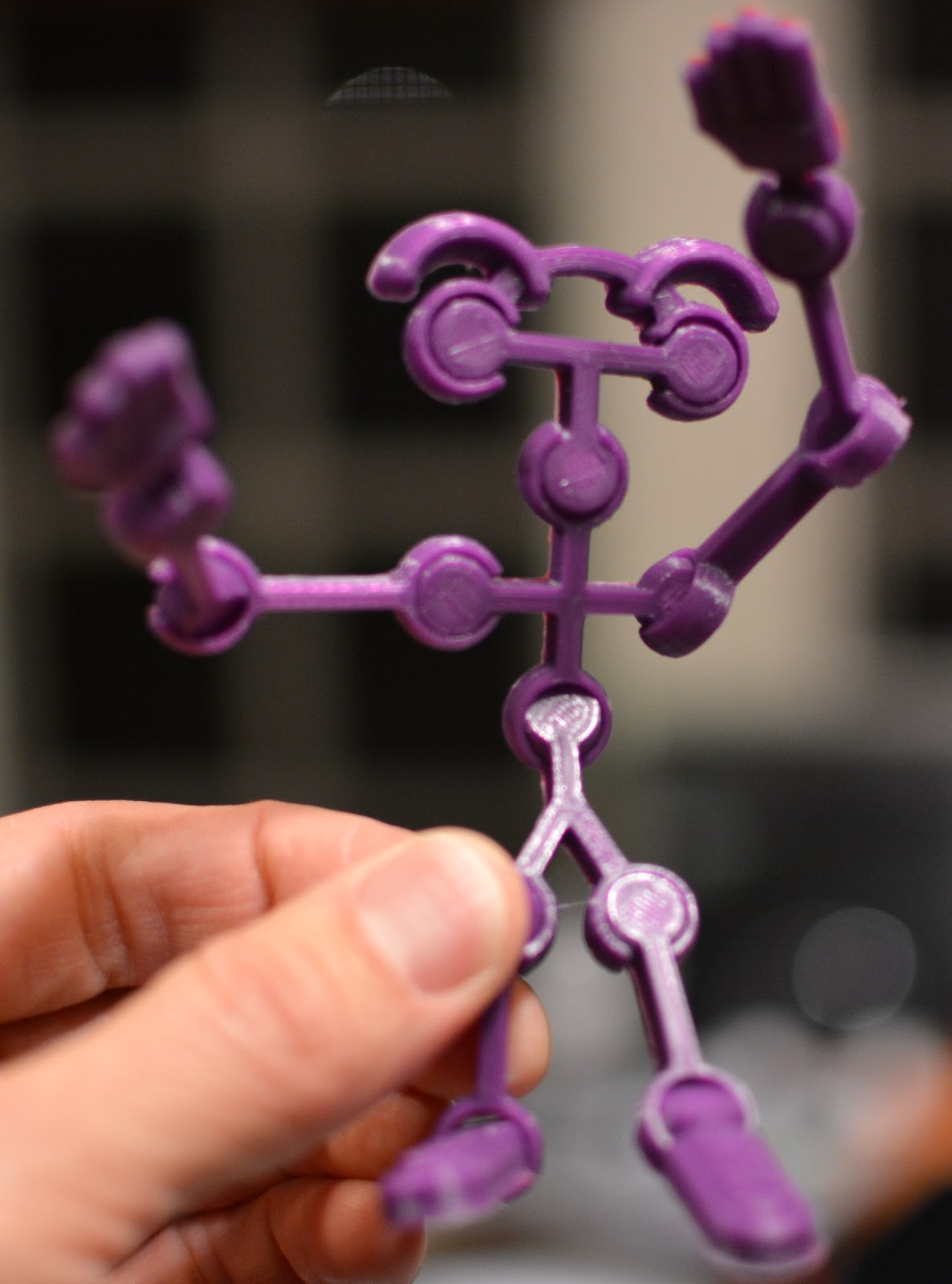
Design For 3d Printing Easy Snap Fit Parts With Maker Club Pinsh 3d printing snap fit joints: how to design & print them. by lucas carolo. published feb 28, 2022. snap fit joints are a great solution for part assembly. read about designing and 3d printing snap fit joints, and more, in this guide. Here are a few different ways that i've made parts that connect in the past: example 1: utilize the elasticity of the plastic by creating a semi circle to fit around another object. when fitting the part to the other object, the "wings" will flex out and relax around the back end of the object. example 2: t slot style designs are a nice choice.
Comments are closed.